Quick Answer
The engineering design process (EDP) is a method of collaboration that allows teams to design, build, and test new products or systems.
How do engineers turn a mere concept into a tangible reality? The answer lies in the engineering design process (EDP).
The engineering design process guides engineers and developers in generating various ideas and solutions and testing their potential. As an iterative process, this method is a useful strategy to create refined market solutions that excel in user experience.
This article will break down the engineering design process and discuss best practices for implementation.
Key takeaways:
- The engineering design process helps engineers break down problems into manageable components, identify potential solutions, and develop innovative designs.
- The EDP’s cyclical approach allows engineers to learn from their concepts, improve their designs, and ultimately create optimal solutions.
- By understanding and utilizing this process, teams can approach problem-solving more systematically and creatively.
What Is the Engineering Design Process?
The engineering design process is a framework for teams to solve problems. It outlines how engineering teams identify a problem, brainstorm solutions, and test ideas and theories. The process is defined yet flexible, meaning teams can adjust goals, ideas, and solutions as they go.
The EDP is a creative and cyclical process where engineering teams collaborate to generate ideas, work together to plan execution, and make, test, and improve on the solutions generated.
8 Steps of the Engineering Design Process
The EDP steps outlined below provide a structured approach to improve team collaboration, and streamline product or system development and design.
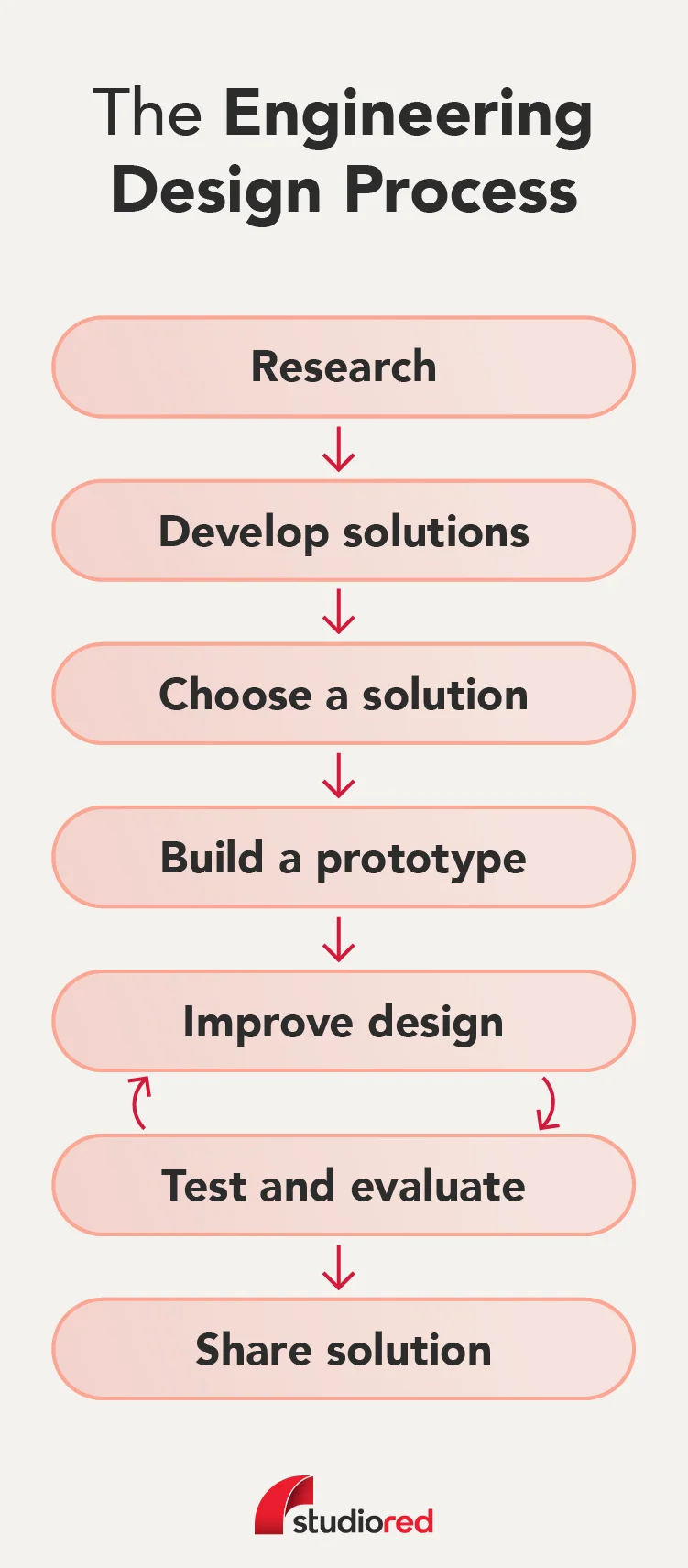
1. Identify the problem
This first step requires your team to identify the problem that needs a solution. This could include analyzing feedback from users or field specialists, surveying a market sector, or internally assessing the effectiveness of an existing product or system.
The engineering design process applies to electrical, mechanical, and civil design challenges. It is also central to product design, as it creates a path toward continual improvement and innovation. The EDP can also be used to improve existing systems, making it valuable in manufacturing process design and quality control systems.
Example:
A beverage manufacturer may receive complaints from consumers about leaks and explosions when their beverages are placed in certain environments, a clear indicator that there’s room for improvement in their beverage carton design.
2. Research the problem
Proper research is a critical step in the engineering design process, as it informs your team’s problem-solving focus and design strategies. Part of the research can include market analysis to determine how a potential solution will be competitive and align with current industry trends.
Thorough research will also help identify the urgency of a solution, such as falling market share or current product development among competitors. This information can set the timeline for a speed-to-market solution.
If your team has identified an industry-wide problem, then the solution developed could become a widely applicable new standard.
Example:
Market research may reveal common complaints stemming from one beverage manufacturer, or maybe they’re focused on a single type of carton or beverage. The team could also conduct store checks to assess the condition of products on shelves or examine how competitors are packaging their products to identify potential weaknesses in their current packaging design or manufacturing process.
This is also a great time to create a product requirements document (PRD), outlining the product’s purpose, target market, competition, and other important details.
3. Develop Possible Solutions
Brainstorming allows engineering knowledge, technical skills, and creativity to contribute to innovative solutions. Working from the problem identified and the completed research, teams can use this step as an open forum to capture ideas.
Example:
Your team is challenged with finding a solution to the integrity of carton lining in uncontrolled environments. Possible solutions could surround packaging design, manufacturing processes, chemical treatments, or material selections. This step gives subject matter experts (SMEs) the space to propose solutions and get input from the team before moving forward.
4. Find the Best Solution
Next, your team can evaluate the ideas generated and identify the best solution to develop. Working together, the team can assess:
- How well the solution solves the problem
- If it is technically feasible
- The cost implications
- Any production challenges, such as the need to change equipment
A review of the research will also inform the team if the solution solves any additional issues or impacts currently well-performing aspects of a product.
Example:
When solving the beverage carton problem, your team may have generated several concepts, from design adjustments to changes in the carton materials. Selecting the best solution would involve addressing regulatory requirements, logistics, production, and costs across a global supply chain. You can also add this information to the PRD you created in step 2.
5. Create a Prototype
The prototype stage of the EDP is where your team’s technical skills are used to model a solution. This can include creating sketches, CAD, or other types of information-rich design plans that can be converted into 3D models and renderings. The prototype captures the most viable solution generated by the team in the previous steps of the engineering design process.
Example:
Once the beverage carton team has designed a prototype, it can be put proto-fabricated and prepared for the next steps of the process. Regardless of the type of prototype, its value comes from the feedback gained, which the team can then incorporate into final product development.
6. Test and Evaluate
When a team follows the engineering design process, the intention is to solve a problem. This stage of the EDP is where the team can test their solution to verify its effectiveness. It’s also an opportunity to test the prototype against existing performance metrics to see if the new model has any negative impacts.
Example:
In the beverage carton example, testing prototypes in different temperatures and affecting settings like humidity would be important data to gather.
7. Improve the Design
The iterative nature of the engineering design process allows teams to evaluate their progress and refine the solution. The testing stage of the EDP can help inform teams of unforeseen problems with a prototype. In some instances, this can help the team adjust the design, or it may mean that a new solution is needed.
Where a prototype fails, the team can return to earlier steps in the EDP, revisit their research, and work through the process again.
Example:
If your team proposed to change a carton material but did not adjust the assembly process, one or both of these issues may need to be resolved before reaching a final solution.
8. Communicate results
As teams move through the engineering design process, it’s important to capture notes and information that can be organized and communicated. This step not only conveys the current solution to product development teams but it can inform other product design teams. Communicating the results of the process can contribute to market-wide safety or quality control improvements.
Example:
If the beverage carton prototype replaced a plastic with a metal, this would have implications for cooking. This type of information would be crucial to the product development team so they can carry this throughout the product lifecycle to the end user.
Best Practices for Implementing the Engineering Design Process
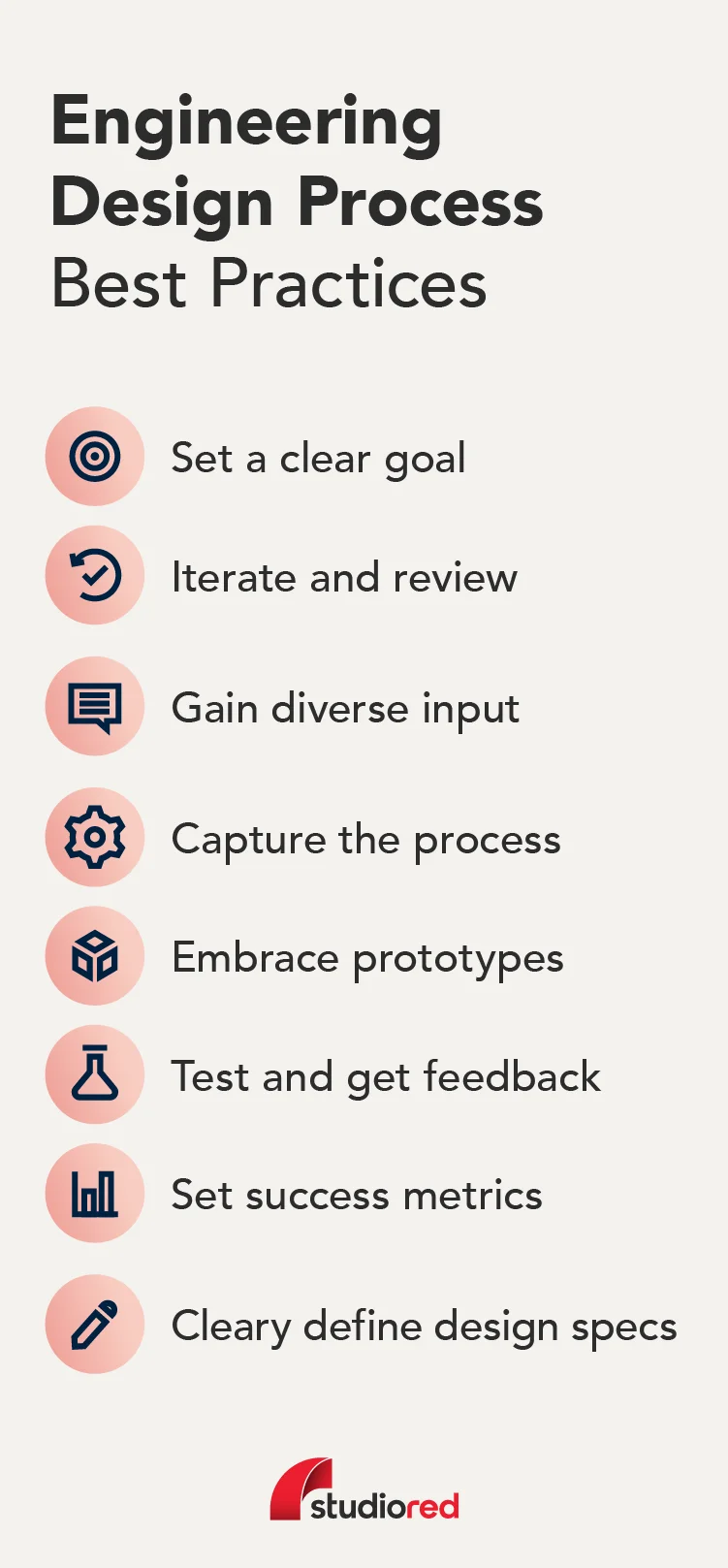
The engineering design process works most effectively when the team implements the intention behind each step. These best practices span industries and applications as a clear framework for teams to work within the engineering design cycle.
- Set a clear goal: Start with a well-defined problem to solve that has a specific market impact.
- Iterate and revise: Expect a trial-and-error process that produces several versions of a solution.
- Gain diverse input: Listen to technical experts, users, and other stakeholders such as client account managers.
- Capture the process: Document the process in full to capture lessons learned, which can inform future design iterations and improve overall efficiency.
- Embrace prototypes: Implement models to prove the success or failure of potential solutions through user feedback.
- Test and get feedback: Conduct rigorous testing to identify and address potential issues early in the design process. Incorporate user feedback to refine the design and ensure it meets the target audience’s needs.
- Set success metrics: Establish clear, measurable criteria to evaluate the effectiveness of potential solutions.
- Define design: Provide detailed design instructions for the product development team to carry forward.
Take a Systematic Approach Toward Innovation
The engineering design process is about collaboration, communication, and innovation. It is a proven method for aligning teams toward clear goals that deliver for clients and users.
At StudioRed, we take pride in our rigorous approach to engineering design, ensuring every product we develop is designed to effectively solve user problems. Interested in how to get your team started? Contact us today.