The impact of virtual design is indisputable but what of the claims in recent years where whole products could be developed in the virtual realm, ready for production release. If we are to believe some of what has been written, a complete new aircraft could be designed in Computer Aided Drafting and Design software, analyzed and optimized, and ready for introduction for service, but would passengers really be disembarking on the first ever physical build of a newly designed aircraft. There are still years of prototypes and test flights before paying travelers are on board, and this is true for most other products as well. In the hype of the benefits of 3D Computer Aided Drafting / Design the benefits of prototyping where pushed aside.
It has been said, “A part is worth a thousand pictures,” and the sooner in the product development effort there is an actual mock-up that can be held in hand the better, as the prototype will allow the development team to learn more and communicate more than they could in just virtual 3D. These first, quick prototypes can provide initial feedback on feel, perceived size, balance in handling (weights can be added to the 3D print or foam to mimic battery and other components inside the product), mechanical functions, and even preliminary real world tests for adequate venting in a housing or bezel. Additionally, the first alpha or pre-alpha prototype can allow for early studies on how the product will fit into its environment in a home, a car, an operating room and so on. These early real world parts are powerful tools for team buy in on decisions, and sometimes funding.
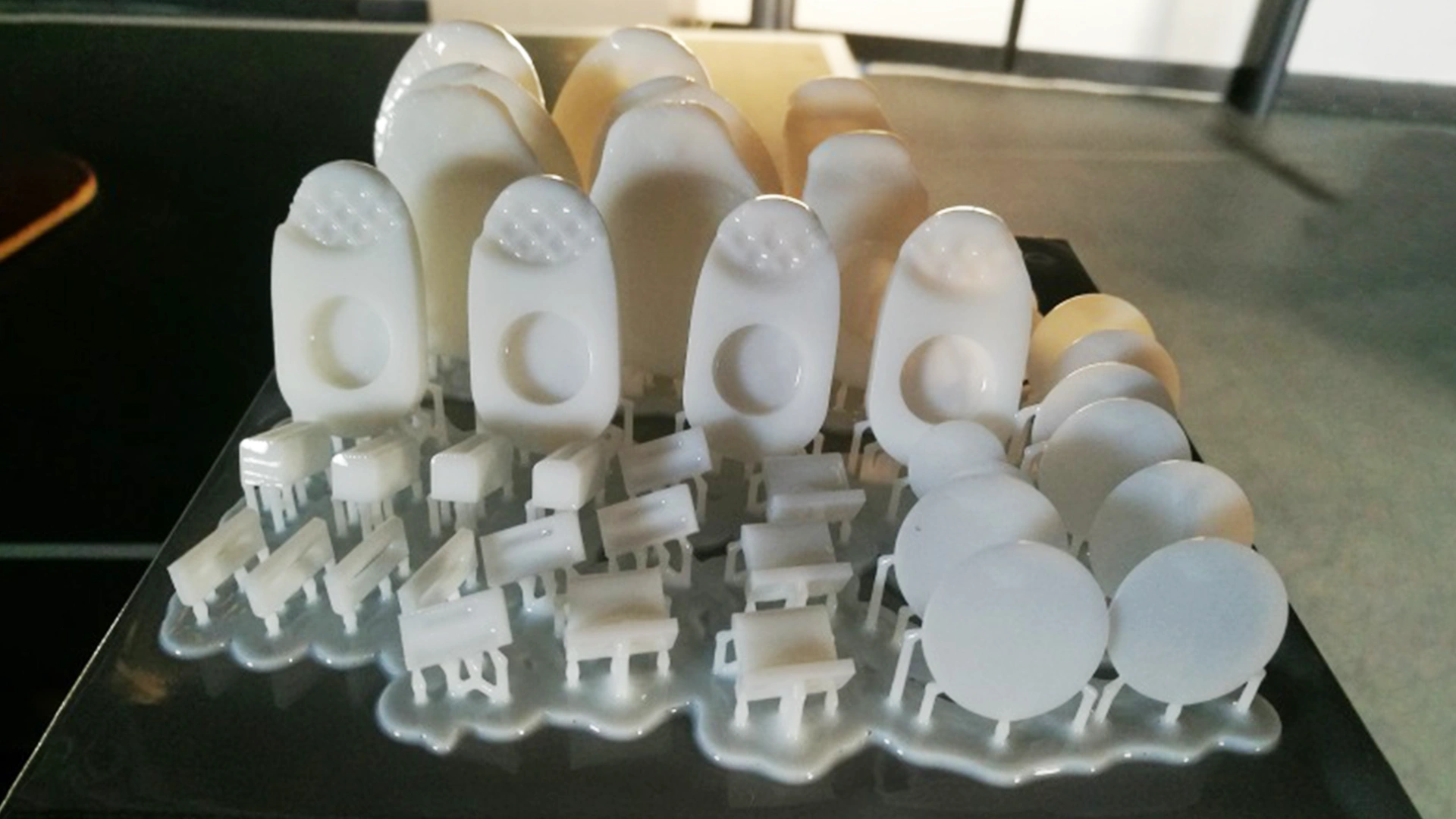
Some might wonder, “But can’t the virtual 3D CAD still quickly produce 3D printed parts for evaluation?” and the answer would be yes, and this should be done sooner than later. Too much on screen time with the CAD can take away from and delay getting to the real world. Early stage mock-ups and prototypes should be produced using 3D printing, hand shaped or CNC machined foam models, or even, very early on, foam core board and cardboard in some cases. This applies whether you are developing a new smart phone or large medical cart. Almost all products have some form of user interaction, even if it is just the installer of the product, and all products require some level of assembly. These initial mock-ups can reveal some “Gotcha’s” when the team actually interacts with the first parts, and the sooner the gotcha’s are caught the less time wasted in development.
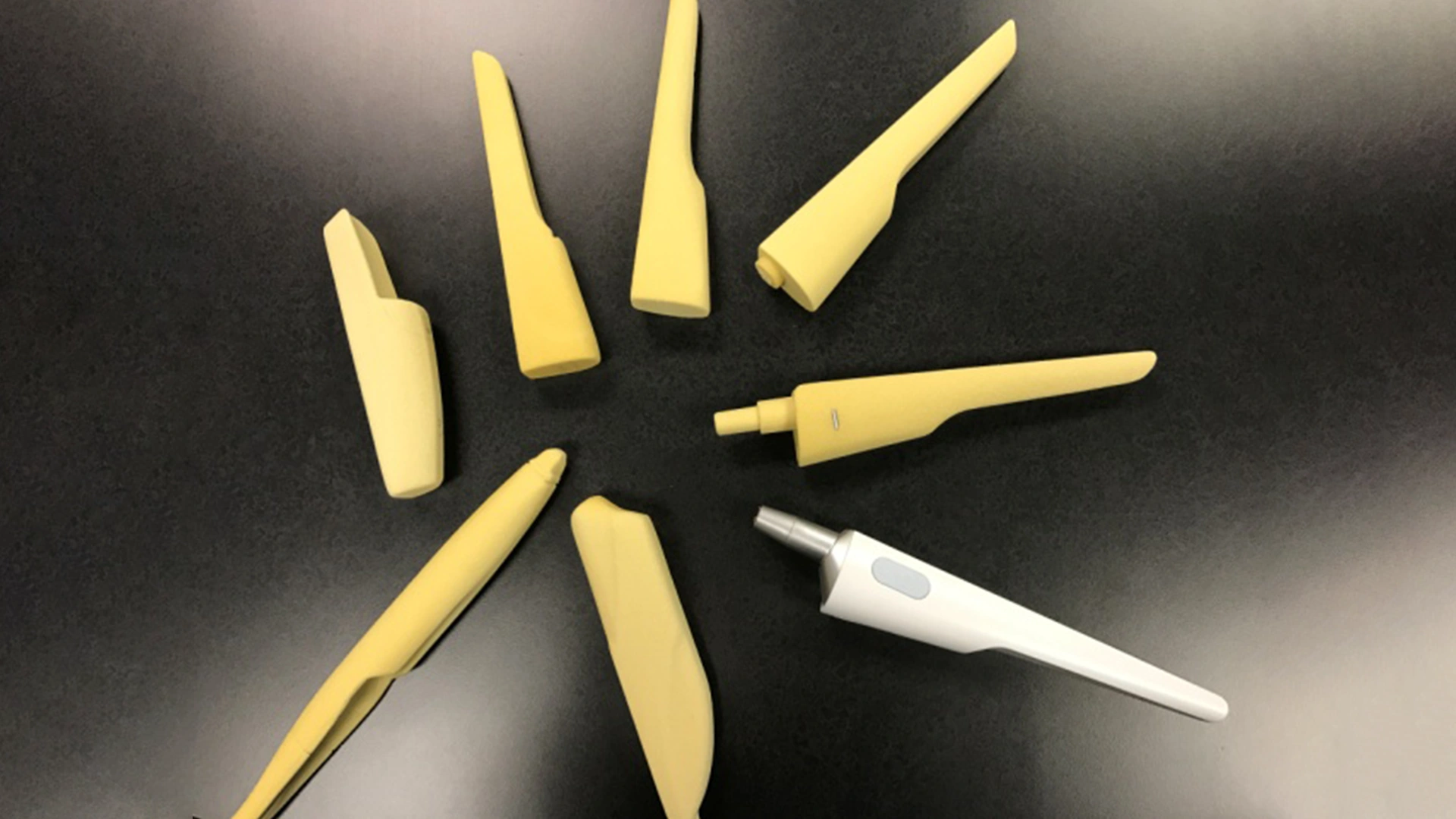
The on screen experience and tools are not always able to fully catch things, even for the more experienced and 3D visually astute. The CAD tools still have their limitations in detection software as well, most notably as the product assembly becomes larger and more complex, and these products can have more issues with late identified gotcha’s and the impact in turn on the development cycle’s schedule.
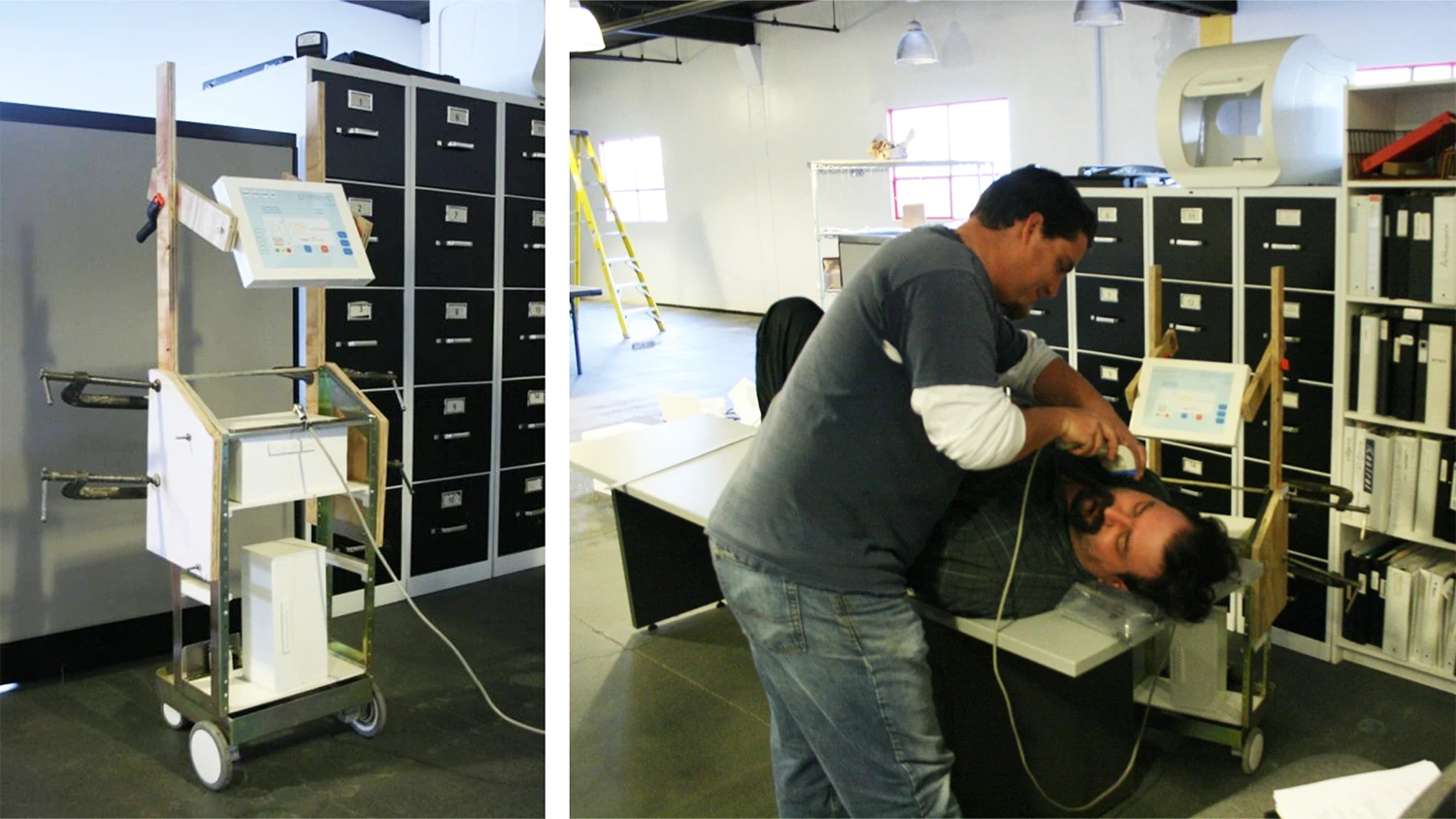
Once an early stage prototype has been made and passed around to development team members, and lessons have been learned from it, then it is time to incorporate these lessons and changes into the product’s design, and be planning for the next prototype, as each new iteration will either prove out the old correction and / or identify new issues to be resolved. Again, these next round prototypes also help communicate to the team the progress and direction. No point in having the marketing director surprised by the size of the final product when it has already been tooled up and entering volume production.
Can you do too many prototypes? Well yes. If the next prototype is not consciously planned to capture the updates then much of its usefulness may be lost. This happens in complex products with fast development cycles, particularly if different design routes are being entertained initially. There should be specific goals for the prototype being built with each version.

Ultimately, the beta prototypes, if true pre-production units should really be in customers’ hands. A successful startup founder even recommend selling the beta prototypes to the initial select user group as this changed the level of feedback as it increased the perceived value and expectation of the user, so there was more feedback provided, and that is what you are really after. It also doesn’t hurt to recoup some prototype expenses if you are starting out.
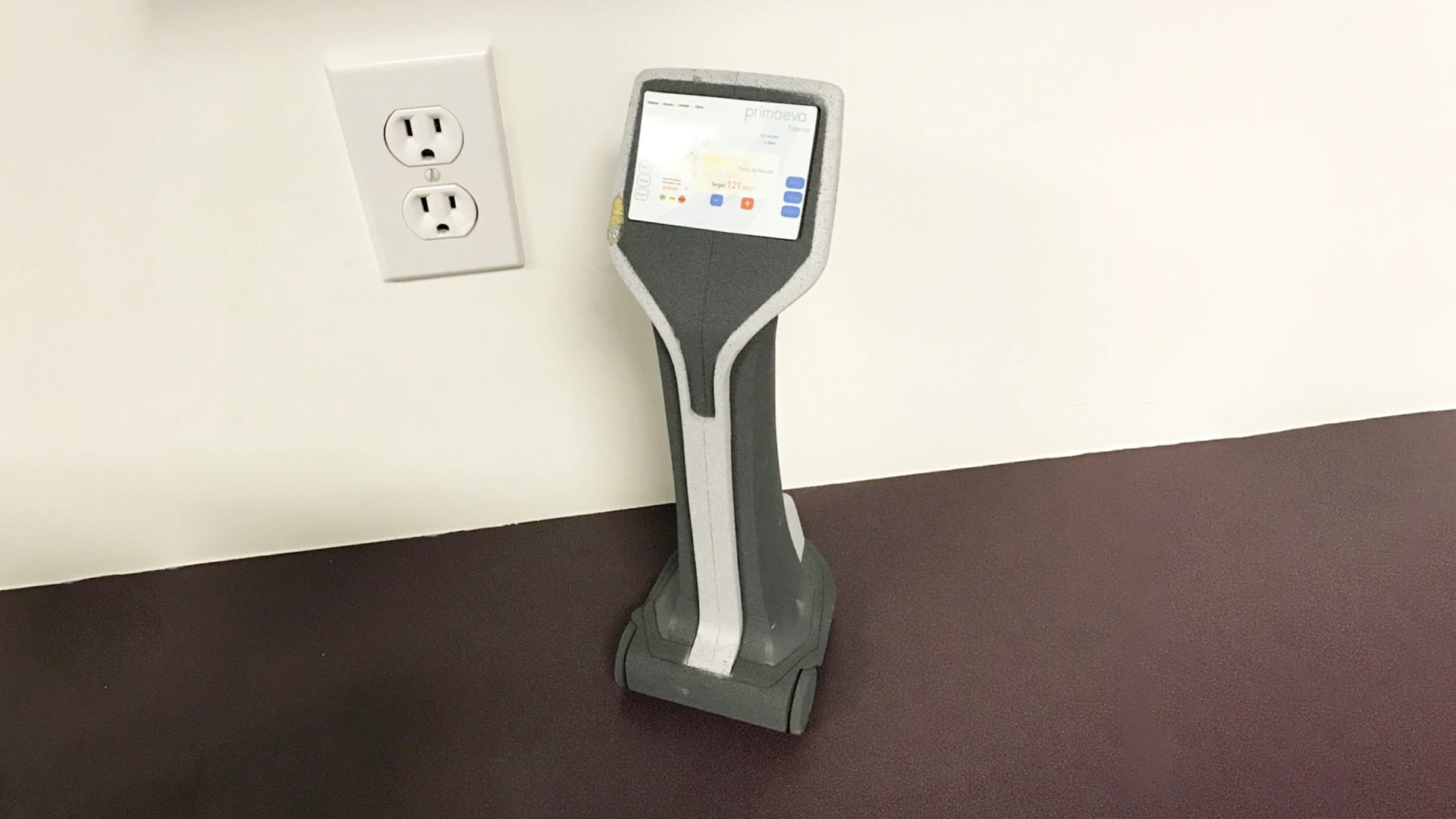
The last key point to keep in mind is there is no perfect prototype. The last pre-production prototype will not be perfect, and its imperfections, again are its value. If it is perfect, then you have waited too long to get to market. Credit needs to go to that same clever founder for that comment. Save something for the next revision of your product.
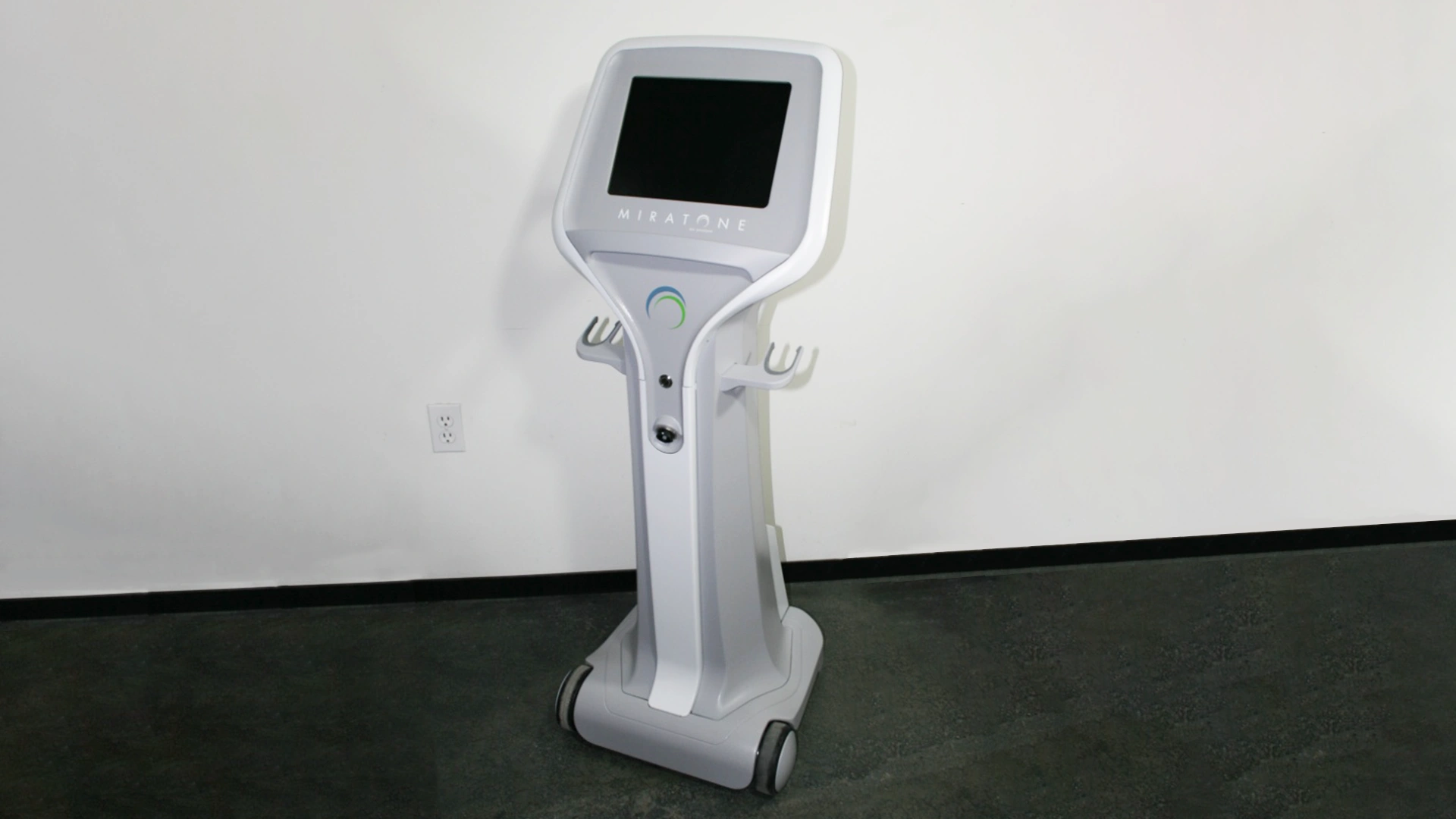
There was a time when all designs were confined to be just on paper with graphically calculated intersection for complex shapes to meet up pieces and to clear components fitted inside, and your company’s in house wood shop would build the first mock-up, all in wood, to check fit up, or how well the new gear design meshed. These wood units would serve as the first prototype mock-ups for fit up and team feedback, the virtual 3D of their time but with splinters. The idea of quickly moving to a 3D prototype held a great deal of value then and still does today. The state of design tools and aids will always progress (what’s coming in augmented reality?) but product design will always benefit from hands on prototypes at all stages of the design cycle.
StudioRed is a full service product development consultancy that helps client’s ideas become realities, and loves making prototypes.