Foam core & foam mock-ups: $100+ (low complexity, quick visualization)
3D printing (FDM, SLA, SLS): $100-$1,000 (varies by method, size, and complexity)
Laser cutting: $25-$100 (mostly material costs, higher with engraving)
Urethane casting: $250-$1,500 per mold, $20-$50 per part (for small runs, additional cost for paint/graphics)
Appearance models: $2,000-$150,000 (depending on size, detail, and part count)
Engineering prototypes: $2,000-$250,000 (complex, functional models for testing)
Low-volume production: $20-$200 per unit (typically for 10-50 parts)
How much does it cost to create a prototype? This is one of the most common questions innovators face — one that can stall great ideas before they take off. Prototype cost is a critical factor in the product development journey, as it can influence timelines, budgets, and overall feasibility.
In this guide, we’ll break down the key factors that influence prototype costs, from materials and complexity to emerging tech trends in 2025. Plus, we’ll share practical tips to help businesses of all sizes effectively plan their budgets and confidently bring their ideas to life.
Why Do You Need a Prototype?
A prototype transforms your concept into a tangible representation of the final product, making it easier to visualize your idea. It allows for real-world testing to identify issues like design flaws, material weaknesses, or usability challenges early in the process before they escalate into costly problems. For instance, a prototype can reveal structural issues that might lead to product failure or user experience hurdles that could deter customers.
By addressing these problems upfront, you can avoid expensive mistakes, such as recalling defective products, redesigning molds, or wasting resources on unsuitable materials. A working prototype can also help secure funding by showcasing the product’s potential to investors and stakeholders with a clear, convincing demonstration.
What Goes Into the Cost of a Prototype?
Several factors influence prototype costs. Here’s a quick breakdown:
- Materials: Costs vary depending on the type and quality, from affordable 3D printing resin to pricier materials like high-grade aluminum.
- Complexity: Simple designs cost less, while intricate products with electronics or moving parts require more resources.
- Labor and expertise: Skilled technicians or engineers charge more, especially for precision work like circuitry or machining.
- Time: Prototypes that take longer to design, test, or assemble naturally cost more.
- Tools and equipment: Accessing specialized machinery like CNC mills or injection molds can add to expenses.
- Revisions: Each iteration to refine the design increases costs due to additional materials and labor.
- Technology: Using advanced tech like IoT components or AI systems often requires more expensive, specialized parts.
How Long Does It Take To Create a Prototype?
Prototype Method | Complexity | Duration | Cost |
---|---|---|---|
Acrylonitrile Butadiene Styrene (ABS) | Low complexity, ideal for early-stage visualization and concept testing | Fast turnaround (typically days) | Starts around $100 for basic models |
3D printing: FDM, SLA, and SLS | Varies from simple to high-precision, functional models | Fast (hours to days) | FDM: $100 for basic, SLA/SLS: Up to $1,000 for complex parts |
Laser cutting | Moderate complexity, used for flat shapes or designs requiring precise cutting | Fast (hours to days) | $25-$100 for materials, higher cost with engraving |
Urethane casting | Moderate complexity, ideal for low-to-medium-volume parts with durability | 1-2 weeks (depending on quantity) | Mold: $250-$1,500; parts: $20-$50 each
Paint & graphics add up to $100 per part |
Appearance models | High complexity, focuses on visual representation of the final product | Medium to long (several days to weeks) | Starts at $2,000 for basic models; up to $150,000 for large, complex products |
Engineering prototypes | High complexity, designed for functional and performance testing | 2-6 weeks or more, depending on complexity | $2,000 on the low end for basic models; up to $250,000 for complex prototypes |
Low-volume production | Varies by method, from simple parts to more intricate designs | Varies (molds take weeks to make and from there parts can be made in days) | $20-$200 per unit, typically for 10-50 parts, depending on complexity and materials used |
Foam Core and Foam Mock-Ups (starts at $100)
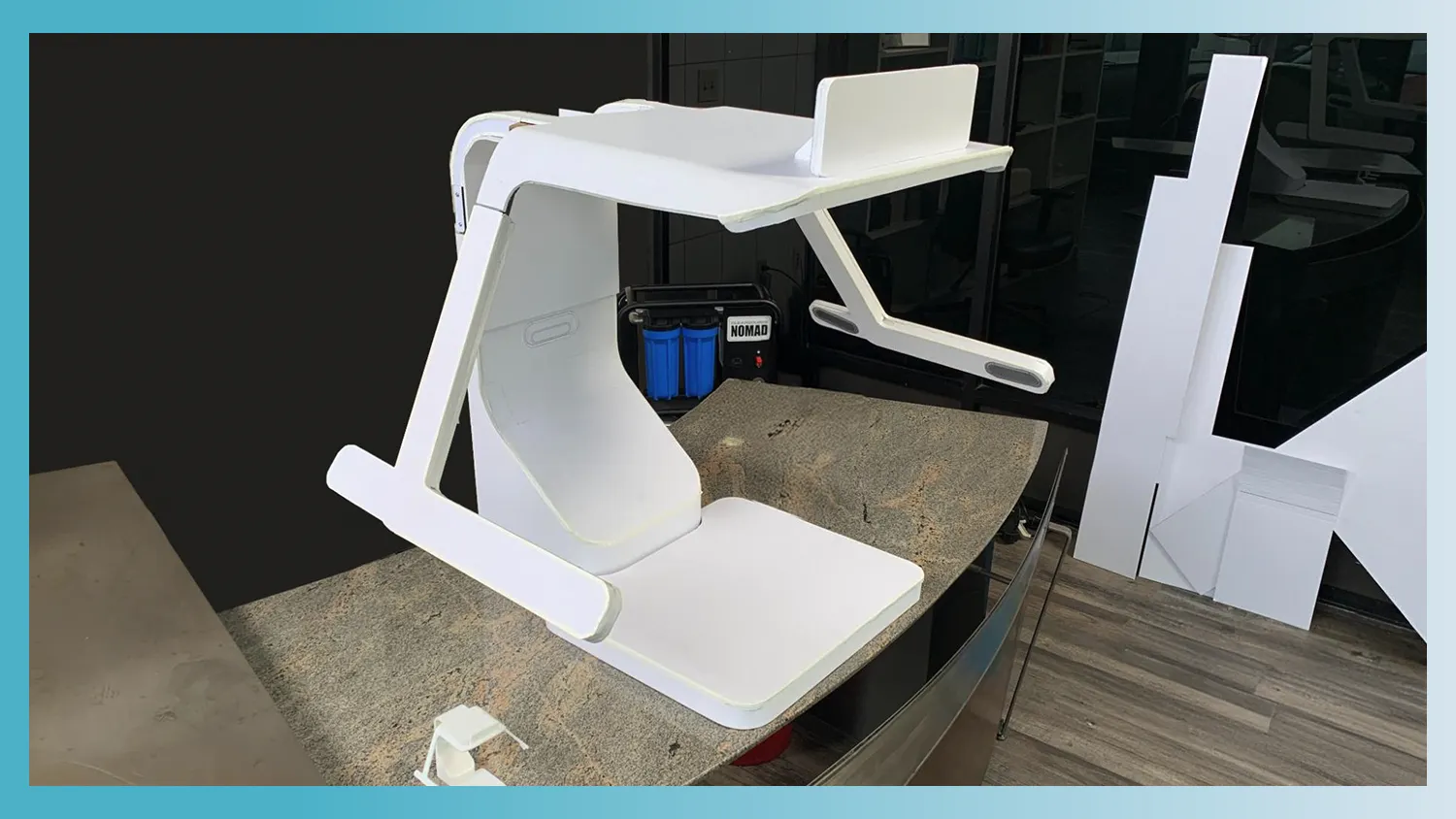
- Cost range: $xx-xx
- Complexity: Foam mock-ups are low-complexity prototypes that focus on shape, size, and basic design rather than precision or functionality.
- Use cases: These prototypes are ideal in early-stage development to visualize concepts quickly. For example, architects might use them to test building models, while industrial designers could evaluate the ergonomics of a handheld device.
- Advantages: Foam prototypes are lightweight, affordable, and quick to produce, making them great for simple designs or getting rapid feedback. They’re ideal for testing shapes, such as packaging or furniture components.
- Limitations: These prototypes are not suitable for high-precision or functional testing. For instance, they can’t test product durability or how components interact with electronics.
- Material variations: Polystyrene is used for quick, affordable prototypes, while polyurethane offers greater density and durability for more detailed mock-ups.
Foam core and foam mock-ups are practical for visualizing ideas in the early stages. For example, a medical device company might use a foam prototype to test the shape and ergonomics of a new handheld device, ensuring it fits comfortably in the user’s hand. These models are made from foam sheets or blocks shaped with utility knives, sanders, or laser cutters for precision.
Their lightweight nature allows for fast iteration and real-time adjustments based on feedback. By refining a product’s shape and size early on, designers can address issues before moving to more advanced and costly prototypes.
3D Printing: FDM, SLA, and SLS (starts at $100)
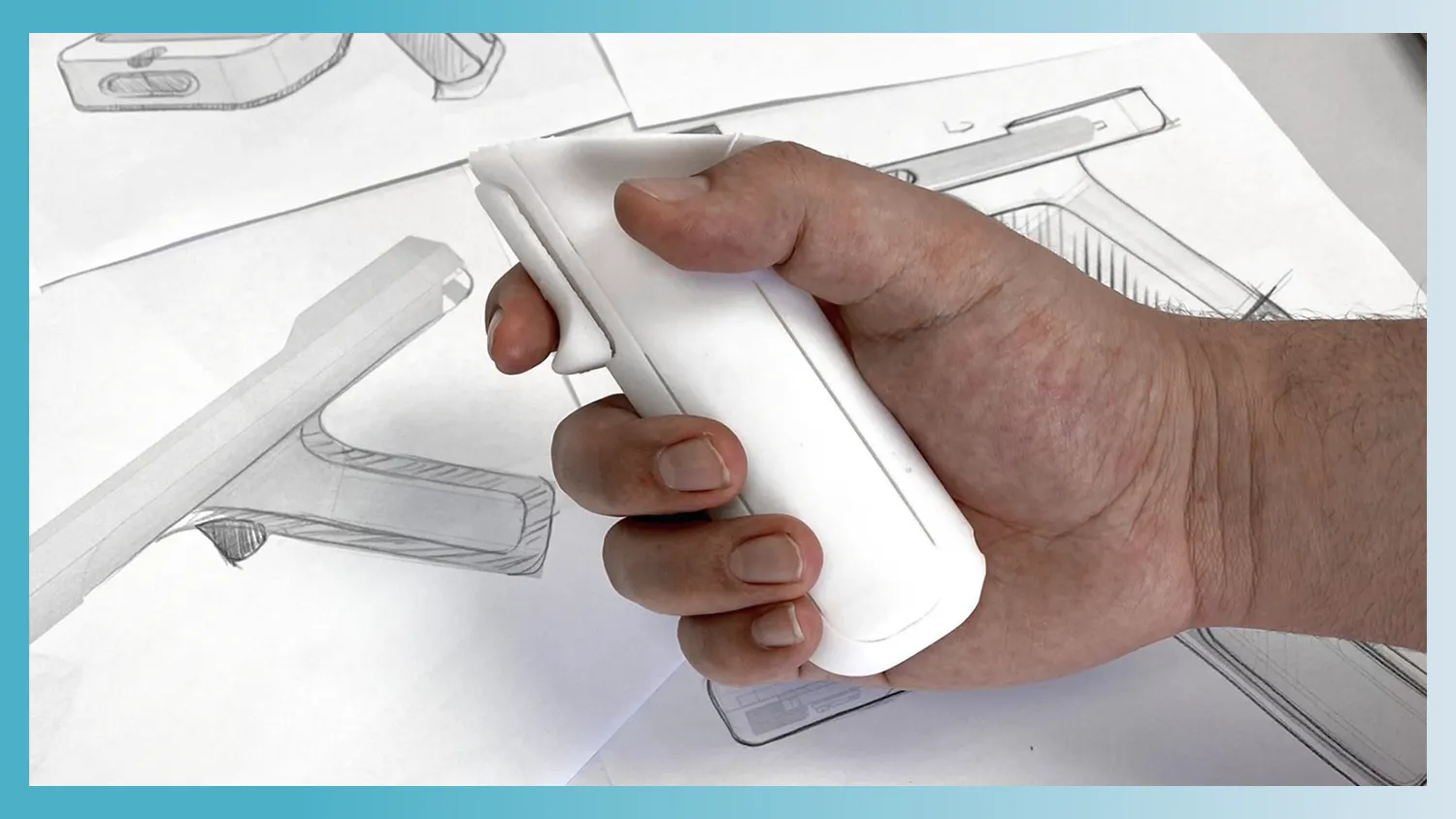
- Cost range: Basic fused deposition modeling (FDM) prints start at $100, while complex selective laser sintering (SLS) or stereolithography (SLA) parts can cost up to $1,000, depending on size and material.
- Complexity: 3D printing can produce simple models or high-detail, functional parts, depending on the technology and how close the prototype is to final production.
- Use cases: These prototypes are ideal for functional testing, rapid prototyping, and small-batch production. For instance, automotive and medical device industries use 3D printing to quickly test parts before mass production.
- Advantages: They’re customizable, quick to set up, and produce low material waste, making them ideal for prototypes needing quick changes.
- Limitations: SLA is slower than FDM, and FDM may lack the precision needed for intricate parts.
- Material variations: SLA uses resins for detailed, smooth surfaces but lacks durability. FDM uses thermoplastics like PLA or ABS, which are durable but less precise.
3D printing is a versatile and cost-efficient method for creating prototypes, particularly when speed and customization are essential. FDM is typically used for simpler, more robust prototypes, while SLA is favored for high-precision, intricate models, like those required in medical or consumer electronics.
SLS, on the other hand, can produce strong and durable parts from materials like nylon, making it a great choice for functional prototypes that require a higher level of detail. With 3D printing prototype costs ranging from $100 to $1,000, this technology allows businesses to efficiently produce prototypes at various price points, balancing cost and complexity based on their needs.
Laser Cutting (starts at $25)
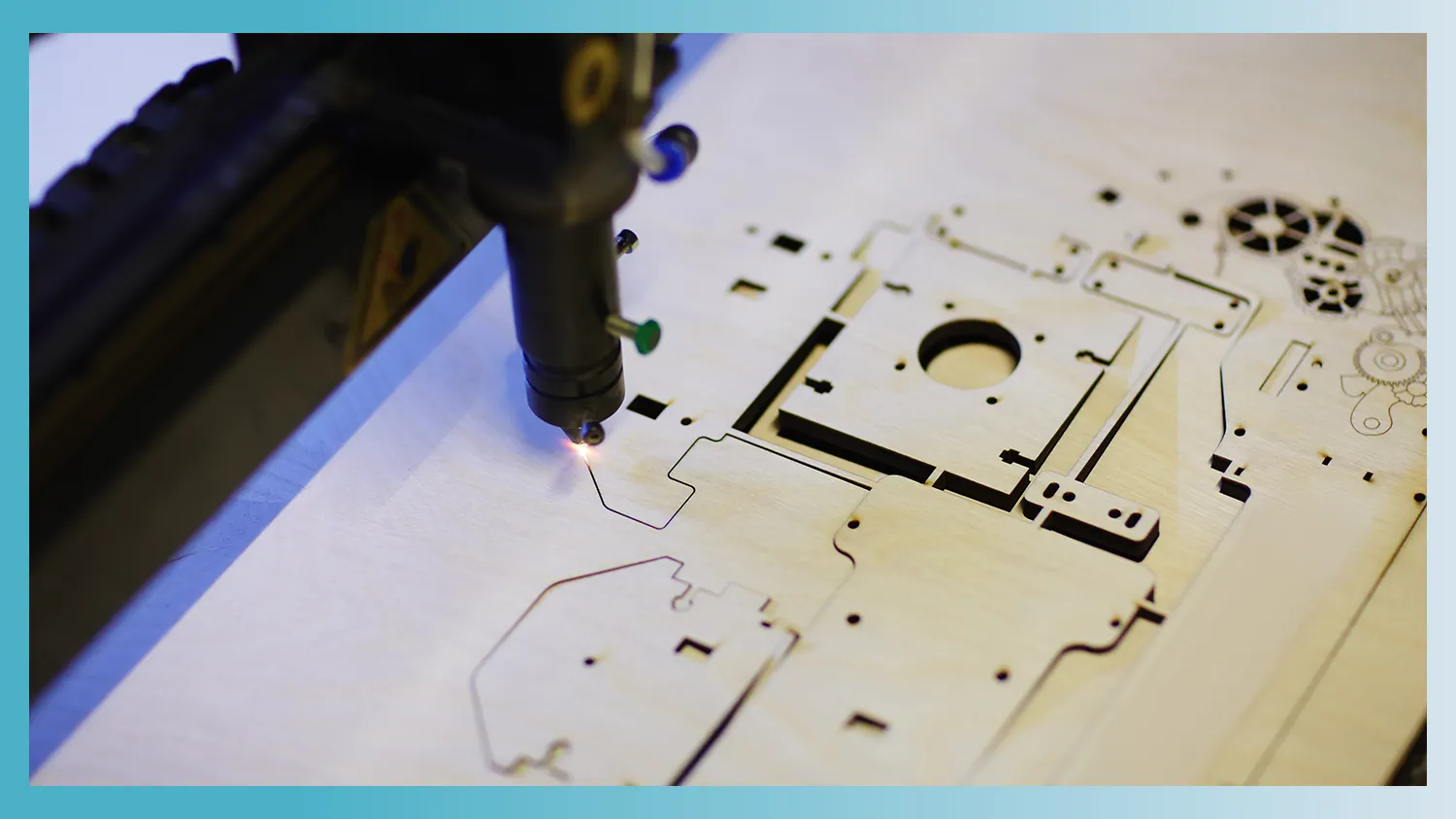
- Cost range: Laser cutting typically ranges from $25 to $100, mostly depending on material costs. On the higher end, laser engraving may also be included.
- Complexity: Laser cutting is best suited for creating precise, flat designs or parts with moderate complexity, usually for prototypes in the early stages or those close to final production.
- Use cases: This method is commonly used for cutting flat parts from materials like wood, acrylic, or metal. For example, it’s ideal for creating intricate signage.
- Advantages: Laser cutting offers high accuracy, fast turnaround, and works with various materials, making it ideal for creating detailed parts without extensive tooling.
- Limitations: These prototypes are limited to 2D shapes, making them unsuitable for complex 3D designs.
- Material variations: Materials like wood, acrylic, and certain metals, such as stainless steel, aluminum, and brass, work well with laser cutting.
Laser cutting is a precise and efficient method for producing flat prototypes, particularly when detail and accuracy are crucial. It uses a high-powered laser to cut through or engrave materials like wood, acrylic, or metal, making it suitable for industries like manufacturing or product design.
While laser cutting is fast and can handle various materials, it’s typically limited to 2D shapes. This means that more complex prototypes requiring 3D shapes or intricate designs must be assembled from multiple parts. Laser cutting is cost-effective for small to medium runs, but material costs can vary based on thickness, density, and type.
Urethane Casting (starts at $20 per part)
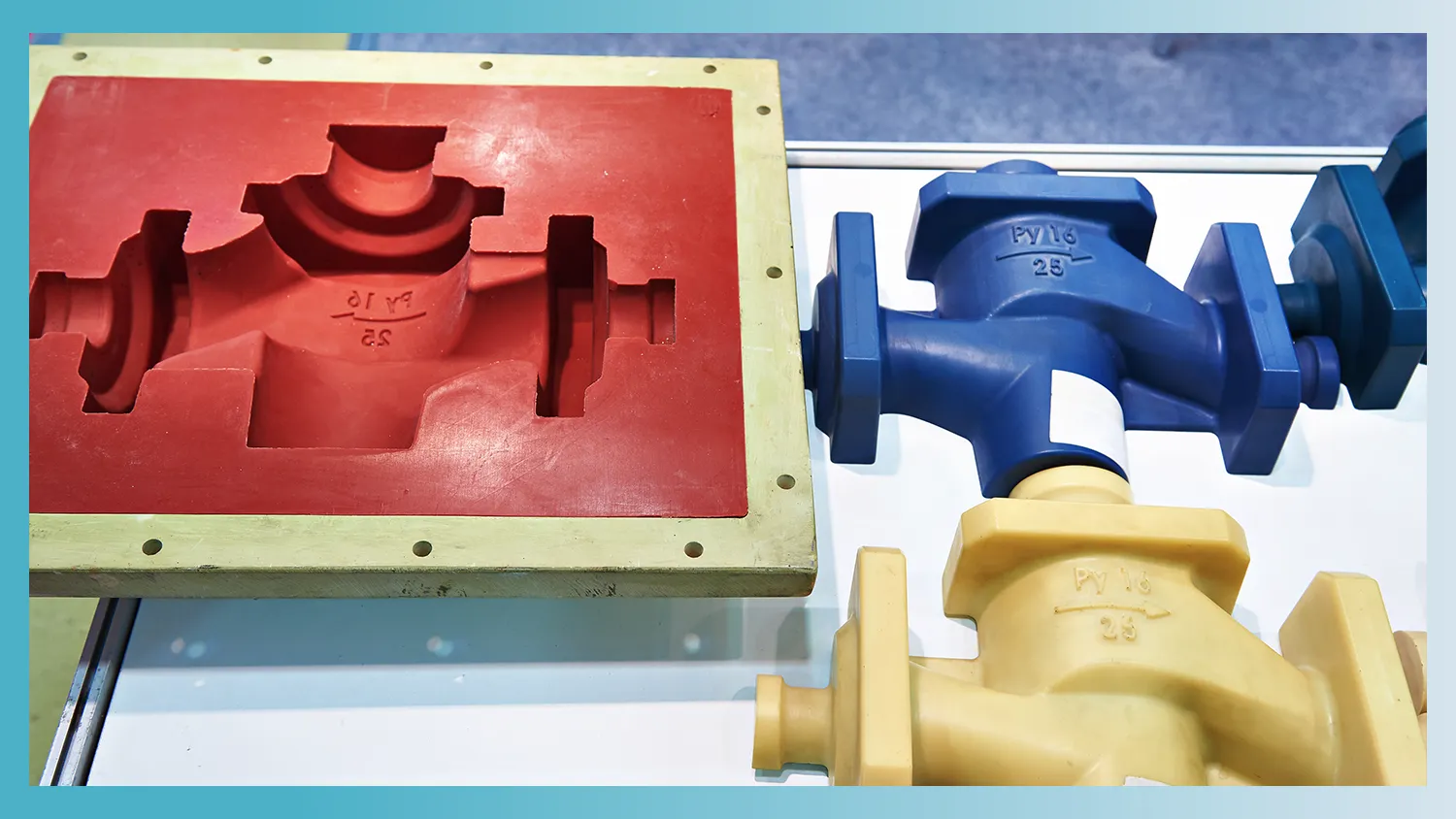
- Cost range: The mold for urethane casting typically costs between $250 and $1,500. Each part costs $20 to $50, with 25-50 parts per mold. Adding paint or graphics can increase the price to $100 per part.
- Complexity: Urethane casting is ideal for parts with moderate complexity. It’s perfect for creating functional prototypes that require durability and detail, such as parts for testing fit, function, or ergonomics.
- Use cases: Urethane casting is commonly used in industries like automotive, medical devices, or consumer electronics. It’s great for low-to-medium-volume production before mass manufacturing.
- Advantages: This method is faster and more cost-effective than injection molding for small runs. It allows for high-detail, functional prototypes that can be tested for real-world usability, fit, and form.
- Limitations: It’s best for parts with relatively simple geometries; it’s not ideal for highly complex shapes or parts requiring specific materials outside of urethane.
- Material variations: Urethane resins vary from flexible to rigid types, providing options for different hardness levels. These materials can mimic plastics used in injection molding but are more affordable for small production runs.
Urethane casting is often used to create detailed, durable prototypes or low-volume production parts. The process involves making a silicone mold from an original part and filling it with liquid urethane resin. This method is cost-effective for automotive, medical, and consumer electronics industries, where prototypes are needed quickly before moving to mass production.
For example, this method could be used to create custom medical prosthetics for patient testing or automotive parts for ergonomic testing. The mold’s upfront cost is higher, but part prices are affordable, making it a good choice for small to medium production runs. While limited to simpler shapes, urethane casting delivers quick results with high-quality details.
Appearance Models (starts at $2,000)
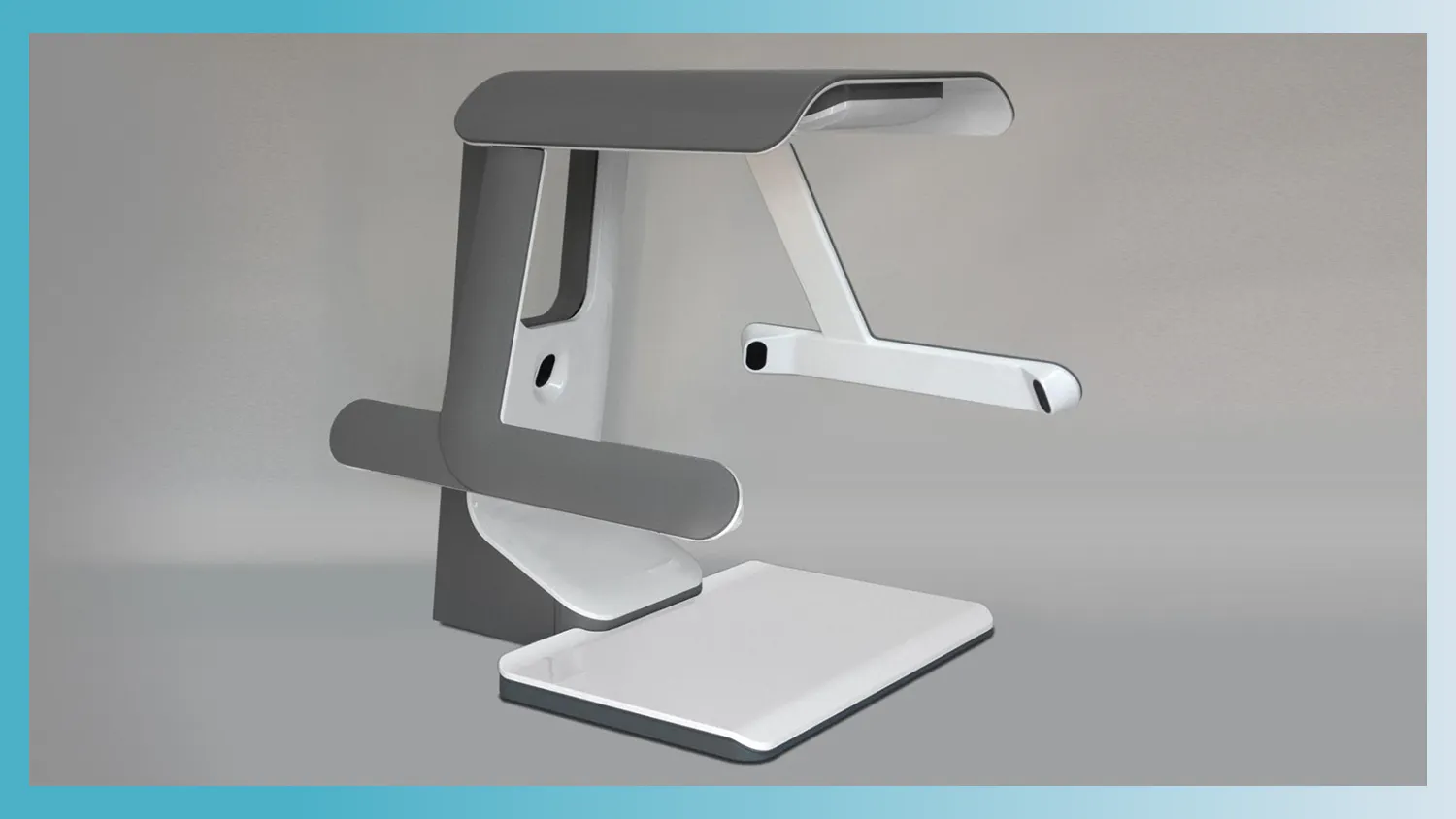
- Cost range: Basic appearance models start at around $2,000. For more complex projects, such as a large product like a refrigerator with 30 parts, costs can rise to $150,000 depending on the level of detail and materials required.
- Complexity: Appearance models are typically designed to closely resemble the final product in terms of shape, size, and color but do not include the functional aspects or internal components. Painting the model can also add to the complexity.
- Use cases: These models are mainly used for visual or marketing presentations, where the focus is on the product’s look and feel.
- Advantages: Appearance models provide high aesthetic quality, making them ideal for stakeholder presentations or product marketing.
- Limitations: While they look great, appearance models are not functional. They can’t be used for performance testing or to assess durability under stress.
- Material variations: The materials used for appearance models can range from basic plastics to high-end resins, with different surface finishes like matte, glossy, or textured.
Appearance models focus on the visual representation of a product and are designed to showcase its final appearance, often for presentations to investors, stakeholders, or marketing teams. They are perfect for situations where the product’s look and feel are paramount, such as trade shows, marketing campaigns, or early design reviews.
Appearance models are not meant for functional testing, as they lack the internal components and materials that make a product fully operational. They may feature high-quality surface finishes and realistic textures, but their cost will vary based on complexity and materials used, ranging from $2,000 for basic models to $150,000 for highly intricate designs.
Engineering Prototypes (starts at $2,000)
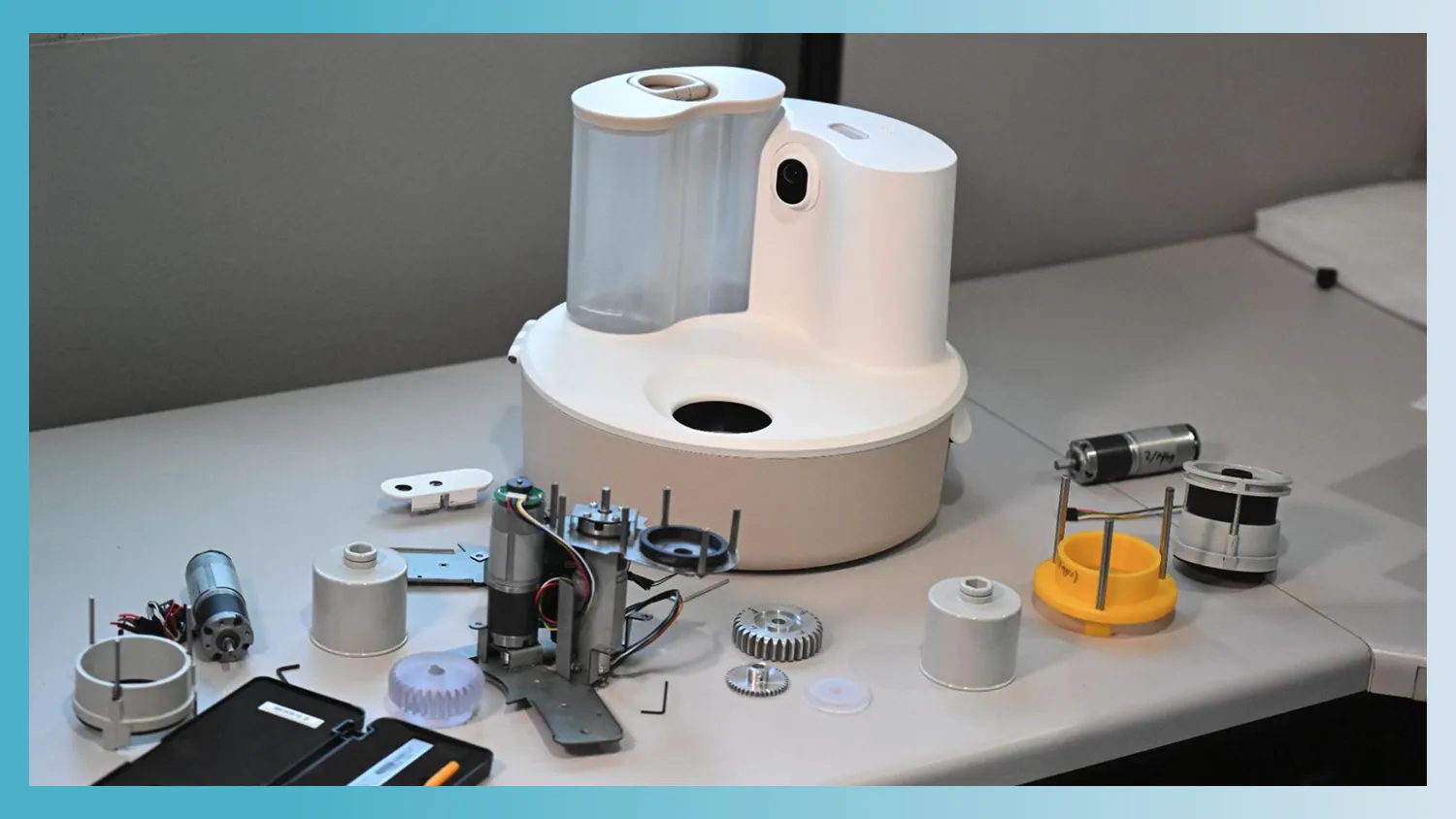
- Cost range: Engineering prototypes start at $2,000 for basic models, climbing to $250,000 for highly detailed prototypes, such as a refrigerator-sized product with 30 interconnected parts.
- Complexity: Engineering prototypes range from simple single-function components to intricate assemblies that closely mimic the final product, including functional mechanisms, electronics, and detailed systems.
- Use cases: These prototypes are ideal for functional testing, engineering validation, and performance analysis in industries like aerospace, robotics, and medical devices.
- Advantages: They deliver real-world performance insights, enable testing under operational conditions, and ensure compliance with safety and quality standards.
- Limitations: This method can be costly and time-intensive due to the need for precision, complex designs, and high-quality materials.
- Material variations: Common materials include aluminum for lightweight strength, ABS for durable housings, and carbon fiber for high-strength, low-weight applications.
Engineering prototypes are designed to replicate the functionality and operational behavior of the final product as closely as possible. They often integrate precise mechanical parts, electronic systems, and sensors to ensure accurate performance testing under real-world conditions.
For example, a prototype of a medical imaging device might include operational software, calibrated imaging components, and housings built to handle anticipated environmental conditions like temperature or humidity fluctuations.
The construction of these prototypes typically involves advanced manufacturing techniques such as CNC machining, injection molding, or 3D printing for specific components. The choice of materials plays a crucial role in achieving the desired performance.
Low-Volume Production (starts at $200)
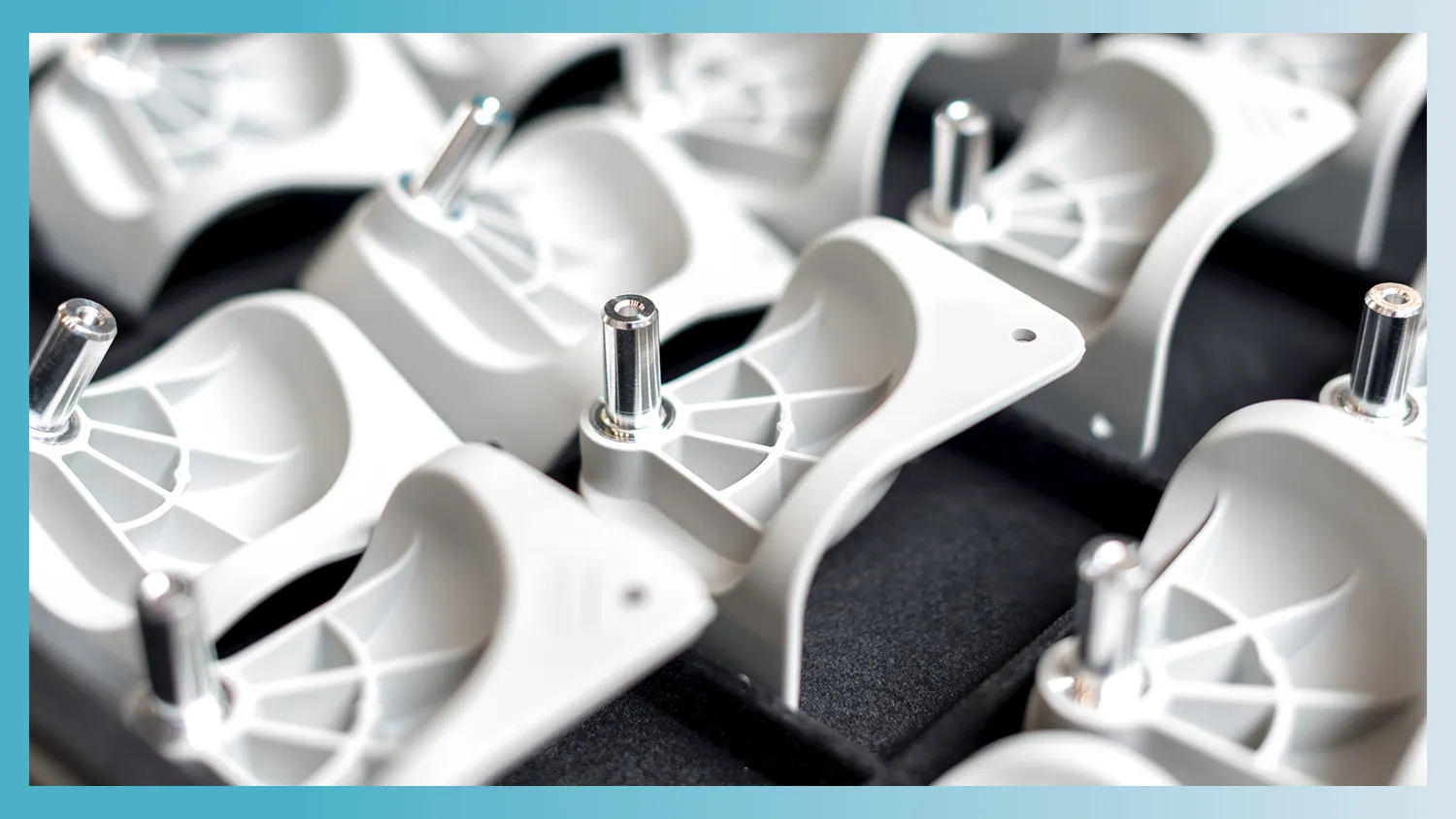
- Cost range: Prices range from $20 to $200 per part, depending on complexity, material used, and the quantity produced, typically between 10 and 50 units.
- Complexity: Low-volume production varies from simple parts to intricate assemblies with precise tolerances, depending on the manufacturing method and design requirements.
- Use cases: This method is ideal for small-scale production runs, such as initial market testing, short-term projects, or creating niche products where full-scale manufacturing isn’t cost-effective.
- Advantages: Low-volume production offers a lower upfront investment compared to mass production, allowing for faster iterations and reduced financial risk for limited runs.
- Limitations: Per-unit costs are higher than mass production, making this method less suitable for large-scale operations.
- Material variations: Materials range from plastics and metals to advanced composites, each offering unique benefits like durability, lightweight properties, or aesthetic finishes, depending on the application.
Low-volume production employs a range of manufacturing methods tailored to specific needs. Injection molding is often used for small plastic parts, where the initial mold cost is justified by producing 10-50 units with excellent surface finish and consistent dimensions.
CNC machining is a go-to option for metal components, allowing for high precision and durability, often favored in industries like aerospace or medical devices. Casting methods, such as urethane casting, are preferred for parts requiring high detail and durability without the overhead of full-scale molding setups.
Transform Your Vision Into Reality With StudioRed
Every great product starts with a bold idea, but turning that idea into reality requires expertise, precision, and a deep understanding of the development process. That’s where StudioRed comes in.
StudioRed specializes in prototype and product development, leveraging decades of experience to deliver exceptional results. Our portfolio showcases many successful projects across diverse industries, reflecting our commitment to quality and innovation.
Whether it’s creating precision-engineered prototypes, visually stunning appearance models, or scalable low-volume runs, we ensure your product meets your needs and exceeds expectations.
Ready to bring your idea to life? Contact StudioRed today.
Prototype Cost FAQ
We’ll address some of the most common questions about prototype costs to help you better understand what factors influence pricing and how to plan your budget effectively.
How Much Does Rapid Prototyping Cost?
The cost of rapid prototyping can vary significantly depending on factors like the complexity of the design, materials used, and the chosen prototyping method. Here’s a general breakdown:
- Low-cost prototypes: Techniques like 3D printing (FDM) can start as low as $100 for basic models.
- Mid-range prototypes: More advanced methods like SLA or CNC machining typically range from $500 to $5,000, depending on material precision and intricacy.
- High-end prototypes: Large-scale or highly detailed prototypes, such as engineering or appearance models, can cost $10,000 to over $250,000, especially for projects involving multiple parts or complex assemblies.
Material choice, finishing requirements, and the number of prototypes also impact costs. Consulting with a prototyping expert can help estimate expenses tailored to your specific project.
What Is the Cheapest Way To Make a Prototype?
One of the most cost-effective ways to create a simple prototype is through 3D printing. This method allows for rapid production of physical models, often at a relatively low cost.
However, for more complex prototypes or those requiring specific materials or finishes, traditional manufacturing methods like CNC machining or injection molding might be necessary, which can be more expensive.
How Much Does It Cost To Develop a Product?
The cost of product development involves a range of factors, including research and development, design, prototyping, testing, tooling, manufacturing, marketing, and distribution.
While prototyping is a significant part of this process, it’s just one component. The overall cost can vary greatly depending on the product’s complexity, target market, and desired production volume.
What Is a Prototype Example?
A prototype is a preliminary model of a product used to test its design, functionality, and user experience. Examples of prototypes include:
- Physical prototypes: 3D-printed models, clay models, or machined parts
- Digital prototypes: Computer-aided design (CAD) models, virtual reality simulations, or interactive prototypes
- Minimum viable product (MVP): A basic version of a product with core features used to gather user feedback and validate the concept