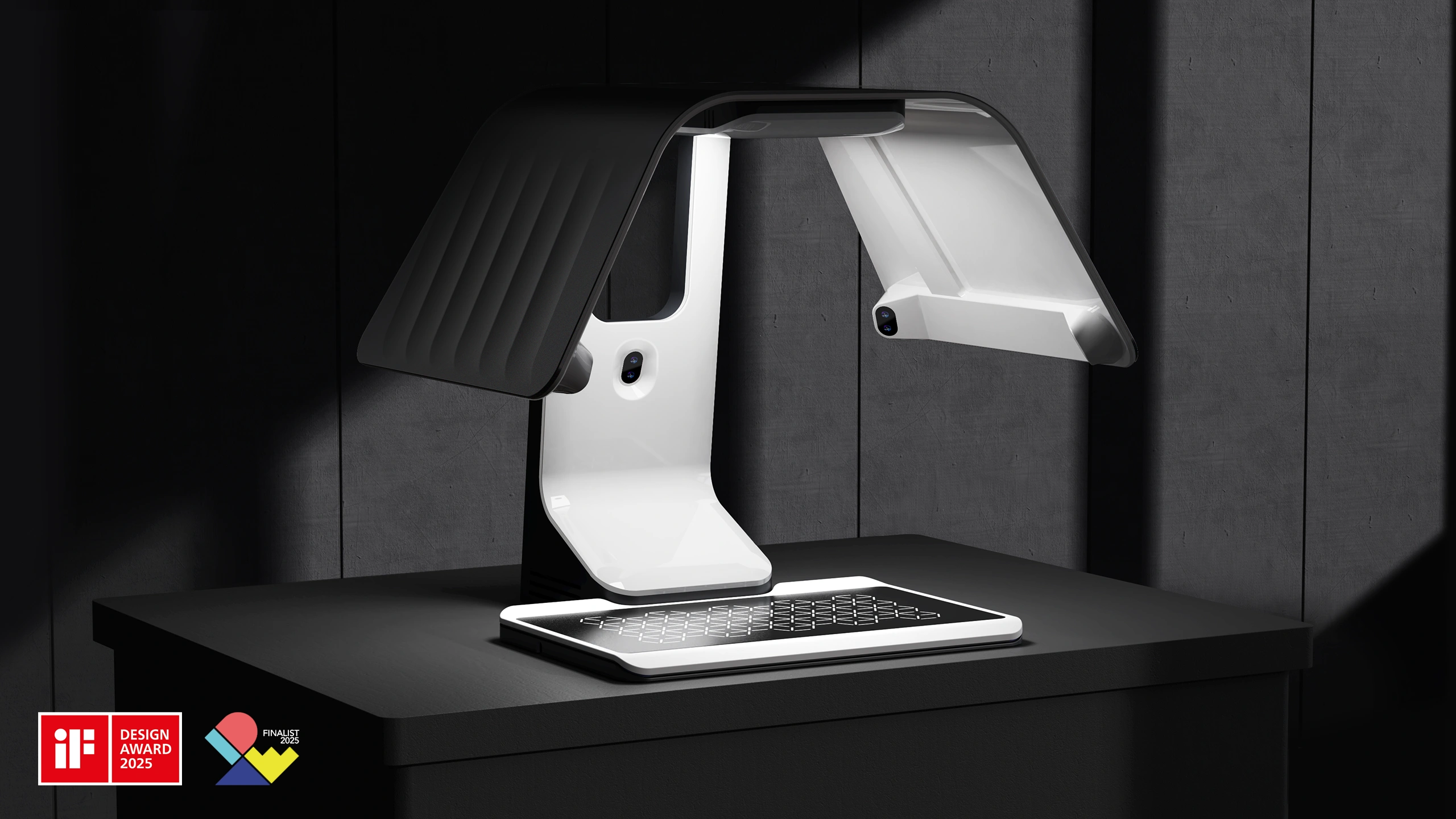
Quick Check-Out
7-Eleven collaborated with StudioRed to develop an automated self-checkout system called the Quick Check-out. This device leverages image processing, integrated Intel depth sensors, and smart scaling to automatically detect items placed on the scale. This innovative system aims to reduce both labor costs and the time required for customers to check out, enhancing overall convenience and efficiency.
StudioRed’s design and engineering team collaborated closely with 7-Eleven’s software team to create the Quick Check-out (QCO) system. This involved multiple rounds of prototyping and user testing to refine the system for optimal performance and user experience. We optimized the placement and configuration of sensors and scales, ensuring the unit’s durability and ability to withstand the demanding environments of 7-Eleven stores.
- 7-11
- 2021-2024
Case study
Efficiency is the key
Customer: be able to interact with cashiers for troubleshooting.
Cashier: the most accessible system to be able to assist customers from behind the unit
Enhanced user experience via sensor configuration
Collaborating with the 7-11 software team to define the optimal sensor package location for an enhanced user experience. By analyzing the positioning of scales and cameras, we considered various worst-case scenarios that could occur during self-checkout.
Balancing structural integrity, ergonomics, and space
To ensure an efficient workflow while store clerks assist customers, it was crucial to maintain open space for easy access to items on the scale, allowing for timely troubleshooting. We developed multiple prototypes to simulate various scenarios, test functionality, and assess how the silhouette translates into a physical object, focusing on visual impact, functionality, and structural integrity. “Creating an unobtrusive Experience” or something like that since we focused on accessibility for both the cashier and the customer.
Distinctive silhouette with integrated tech package
Our design challenge was integrating a tech package with a distinctive and memorable silhouette that stands out in the cluttered environment of a 7-11 store. Throughout the process, we sketched and built quick mock-ups to test the feasibility and viability of our ideas.
Refining form to enhance uniqueness and impact
During the design process, we explored a variety of possibilities and perspectives to gain a comprehensive understanding of potential solutions. This approach allowed us to evaluate different ideas and approaches, ensuring that we considered all viable options. By systematically assessing each possibility, we identified the most effective solution that best met our objectives.
CMF selections
The final metal bead blast finish imparts a premium and advanced feel to the quick checkout unit. The dark color is subtle yet enhances the appearance of the internal components where users interact, creating a balanced and sophisticated aesthetic.
Performance optimization through design details
At each stage of refinement, we assessed whether improvements could be achieved through software or hardware adjustments or if minor design tweaks would suffice. To enhance the accuracy of sensor recalibration with each use, we discovered that incorporating a visual pattern significantly reduced false results and facilitated quicker checkouts. We collaborated with the software team to fine-tune this visual pattern for optimal performance.
Seamless Integration
As the project evolved through continuous testing, sensor and scale placement was adjusted to achieve optimal performance in coordination with the external software team at 7-11. While optical & software engineers fine-tuned the best sensor locations, Industrial Designers ensured that these updates were seamlessly integrated into the design, maintaining balanced proportion and enhancing the overall user experience.
Real world testing & feedback loop
We went through multiple rounds of refinement, building and testing functional prototypes in real-world scenarios. With each iteration, we gathered user feedback to enhance functionality and optimize performance.
Optimized Vision System Integration design
Support client on vision system positioning, camera module integrated custom mountings per Intel and vendors, updates for improved access for user interface, and all geometry controlled through a master model.
Structural Design Optimization
Structural design and analysis, including assessing vibration responses, to meet initial determined loading and industrial design objectives for the user experience. Ongoing updates and frame refinements as camera stability needs matured and work with the contract manufacturer provided further design for manufacturing feedback, while maintaining the intended industrial design look of the PoS station.
Custom plastic housings with Integrated Electronics, and Streamlined Part Geometry for Manufacturing Efficiency
Custom plastic enclosures with complex hidden mountings supported electronics and weight sensing integration with interconnections integrated—refinements for complex parting lines, molding draft requirements, and part count simplifications.
Integrated Venting Solutions
We incorporated open-area venting configurations for various computing and lighting needs.
Full documentation and Manufacturer support
Our engagement included aligning the final product with design objectives while optimizing cost, quality, and efficiency for transition to production. It included comprehensive Design for Manufacturing (DFM) feedback, prototyping and assembly, tooling and production support, quality control, and supply chain and logistics coordination.