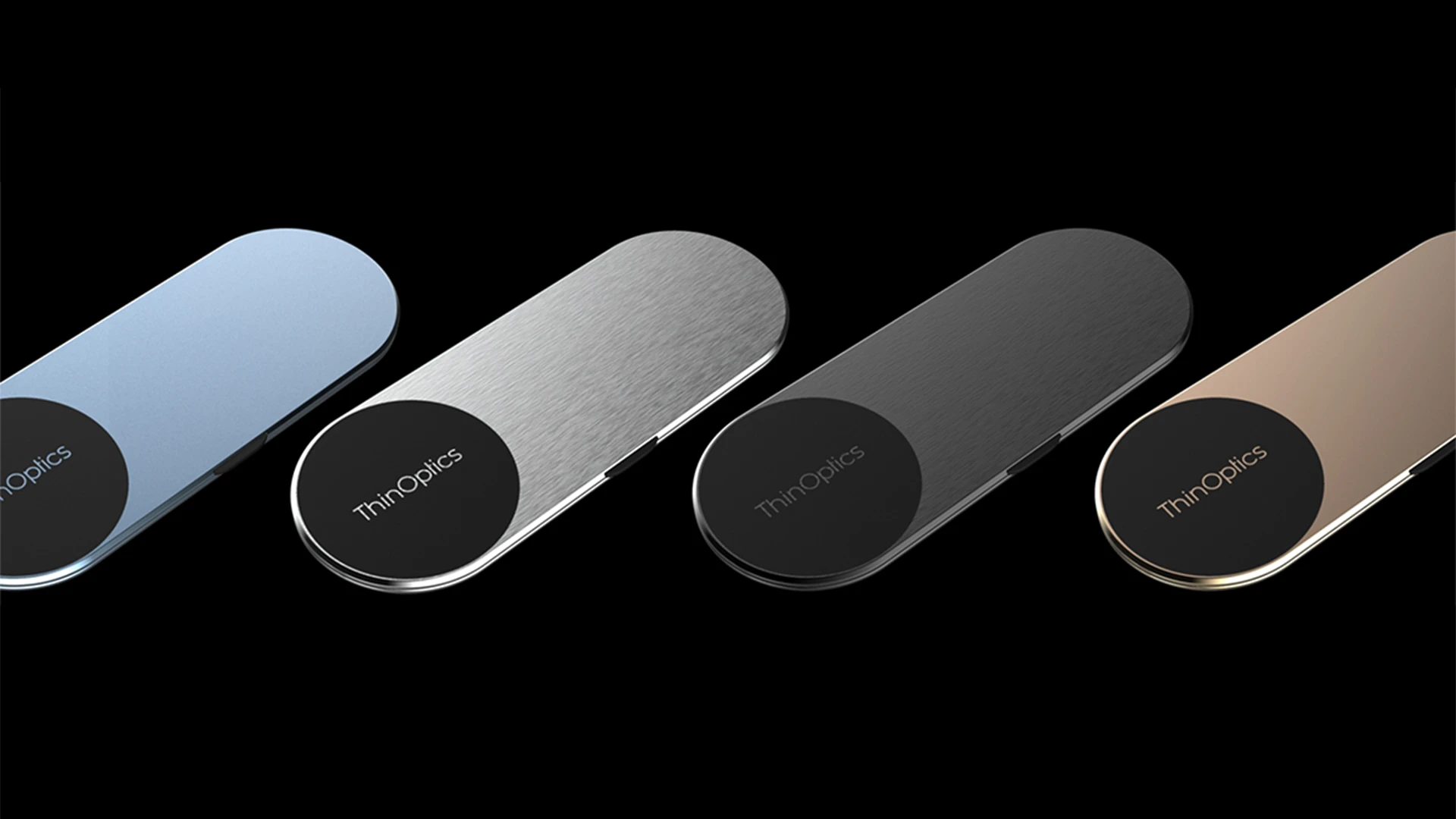
ThinOptics – Manhattan
Manhattan is an ultra-slim case for the ultra-minimal Thinoptics glasses. StudioRed was challenged with the task of creating a functional and portable case with a high-end jewelry-like look and feel. It had to be minimally thin, while being manufacturable all while fitting onto the backs of phones without interfering with back-cameras.
ThinOptics glasses are flexible. The ultra-flexible titanium alloy bridge is made from Nitinol (10x more elastic than spring steel) and easily twisted into small places without harm. They are designed to bend without breaking so StudioRed helped to enclose them in the smallest possible yet sturdiest case.
StudioRed faced many challenges in designing the glasses case. The first challenge was that the case needed to accommodate two types of glasses (circular and rectangular). Various orientations were studied, and one was chosen to fit both types.
Another challenge was building the case so it could fit on the back of various phones and sizes without impeding the camera lens viewing angles. Samsung Galaxy and iPhone 10 were studied and maximum dimensions were determined based on fitting on both phones. Another issue this posed was material selection and avoiding the use of magnets as they would interfere with the phone’s signal.
The client’s requirement of 4 mm thickness was another hurdle we overcame. Because of the thickness of the glasses themselves, there was a very limited selection of materials that could be used, and 0.3mm Stainless Steel was chosen as it met strength and thickness requirements.
- Thin Optics
- 2017
Sculpting the case to fit within 4mm thickness was a challenge, but in the end, through all the restrictions, we were able to create this iconic form factor and elegant design.
Using this material we were also able to design a hinge that could be formed through the stamping process. Using LCP (liquid Crystal Polymer) we designed a plastic assembly, over molded into the stainless steel housing which also created features for a latch that fit within the 4mm requirement.
Working directly with manufacturers was necessary to identify those which had the capabilities to build this case, and could deliver the final flawless surface finish.
The Manhattan case design was a difficult struggle to fit an enclosure around two different glasses while remaining within the footprint of certain iPhone models, while also adding less than 1.5mm to the thickness of the glasses.
This was achieved by using formed sheet metal for the majority of the body with an LCP (liquid crystal polymer) overmolding to provide structure and mounting positions for the latch. This manufacturing method is borrowed from PC cards where compact and robust solutions are essential, making it a great match for this product which will see a variety of environments.
In order the meet the design goals we had to push many of traditional limits of sheet metal forming, LCP overmolding, and assembly processes so it was very important to work with vendors early on to make sure the final design could be manufactured. By having frequent design reviews we were able to have buy-in from the vendor before sending final files out for DFM (Design for Manufacturing).