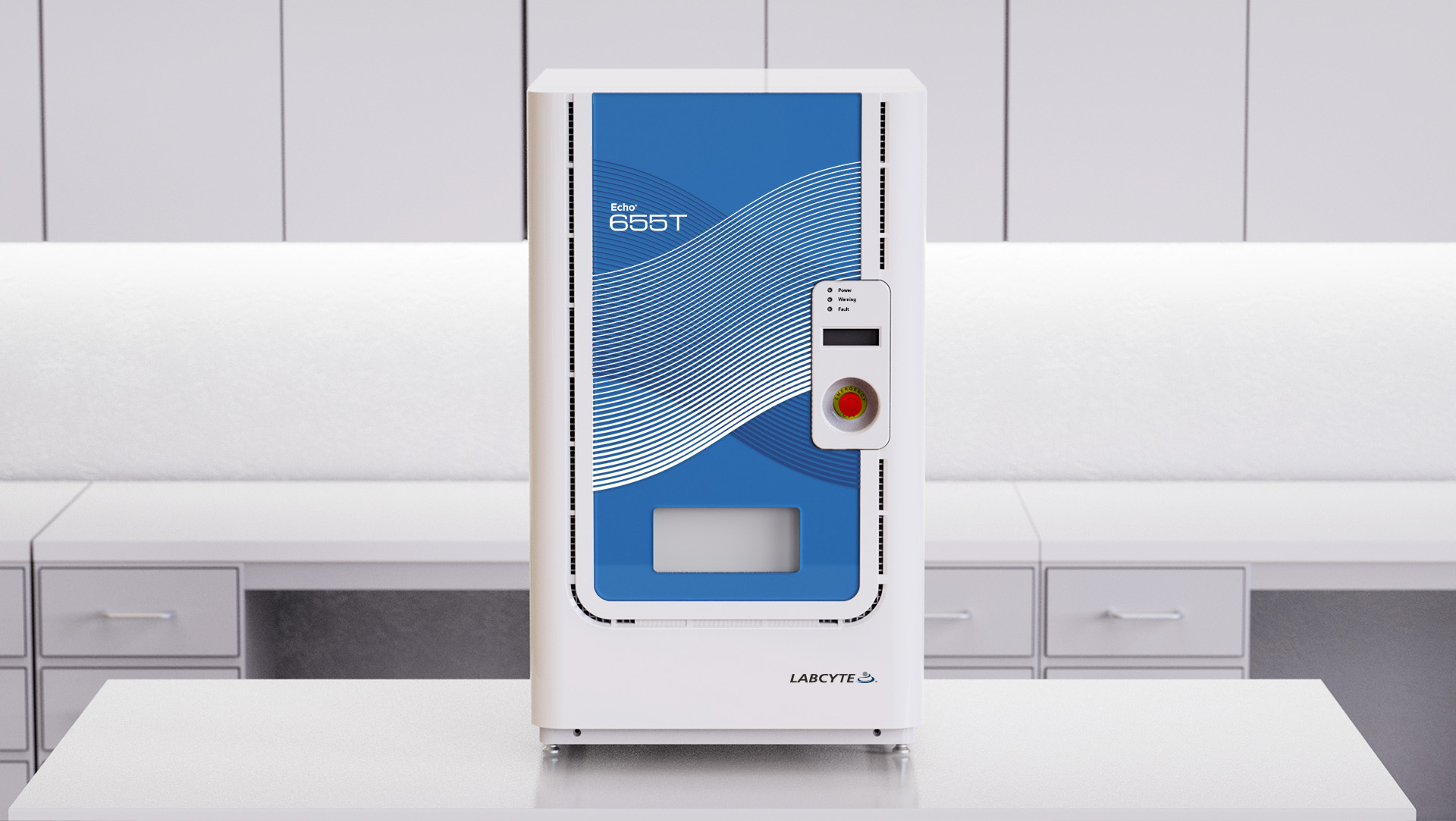
Labcyte Echo
Echo 655T is a biotech system offering revolutionary liquid handling using sound to precisely affect liquids. After developing the overall brand language of Labcyte on an earlier system development program called the Access DRS, our team extended that language to this new system based on our client’s unique functionality. We illustrated their sound technology as a visual wave on the front and rear faces of the 655T to be iconic and memorable. Along with challenging robotic limitations, sealed doors and limited space, uniquely with the Echo line, user faces the back side of the product often. StudioRed applied a simple element(s), materials and graphics to visually upgrade the back of the product because we believe every touch point of the product should be considered. Throughout the program we met unique mounting, thermal and air flow requirements along with full EMI containment and produced all component parts with methods that fit the low production quantities of the system.
- Labcyte
- 2017
- Good Design Awards, Spark Design Awards, SLAS 2018
Earlier Concepts
Back of the Product
Color/Graphic variation possibilities for different Echo models.
In the device there is an articulated arm to rotate the sample trays for the acoustic processing. Initially there was an extremely tight length of travel constraint that meant the front panel could only be 3mm thick in the area where the arm would rotate, given the 6mm thickness of the PC panel there we only one path forward: to locally pocket the panel. The issue with doing this is that the panel must be machined and as such cannot be economically polished to the same level as the stock surfaces around it. A pocket with a planar bottom would have very obvious and unsightly swirls from the machines cutter. To hide these marks we decided to make them a feature, by using a ball end-mill rather than a flat end-mill we created a series of ridges that would serve to obscure the imperfection of the machined surfaces.
Main challenge: fastening PC with limited thickness and no visible fasteners:
The ID called for a inset/transparent PC panel that is planar with the surrounding bezel, to complicate the issue there were severe space constraints due to the movement of the robot arm so attachment had to be done in a minimal space.
Material was already defined as it is a custom color and specific to the client, available only in 6mm thickness. The design required a opaque planar surface behind the PC to reflect light, however the mechanical constraints meant there was only 1.5mm of space to provide that opaque surface and attach the material. Initial plans were to attach the backing plate using an adhesive, but as the PC is used for branding, the client wanted it replaceable without dealing with adhesive.
There were 3 specific issues:
- How to have the PC planar with its surrounding bezel
- How to provide an separate opaque surface behind the PC, without adding more than 1.5mm
- How to attach the PC in a removable way, without visible fasteners.
They were addressed as follows:
- A flange was milled around the perimter that would allow the front surface of the PC to sit planar with the surrounding beze
- A 1mm thick aluminum back plate that could be painted was used to provide the visual surface behind the PC.
(image showing real panel) - The PC was clamped in place by the back plate using a series of screws hidden behind the bezel, small “keyhole” fasteners kept the back in contact with the PC where there was no room for fasteners. By angling the assembly in place it could be secured without any visible fasteners.